Robotic Printing Clay Formwork for Concrete Casting.
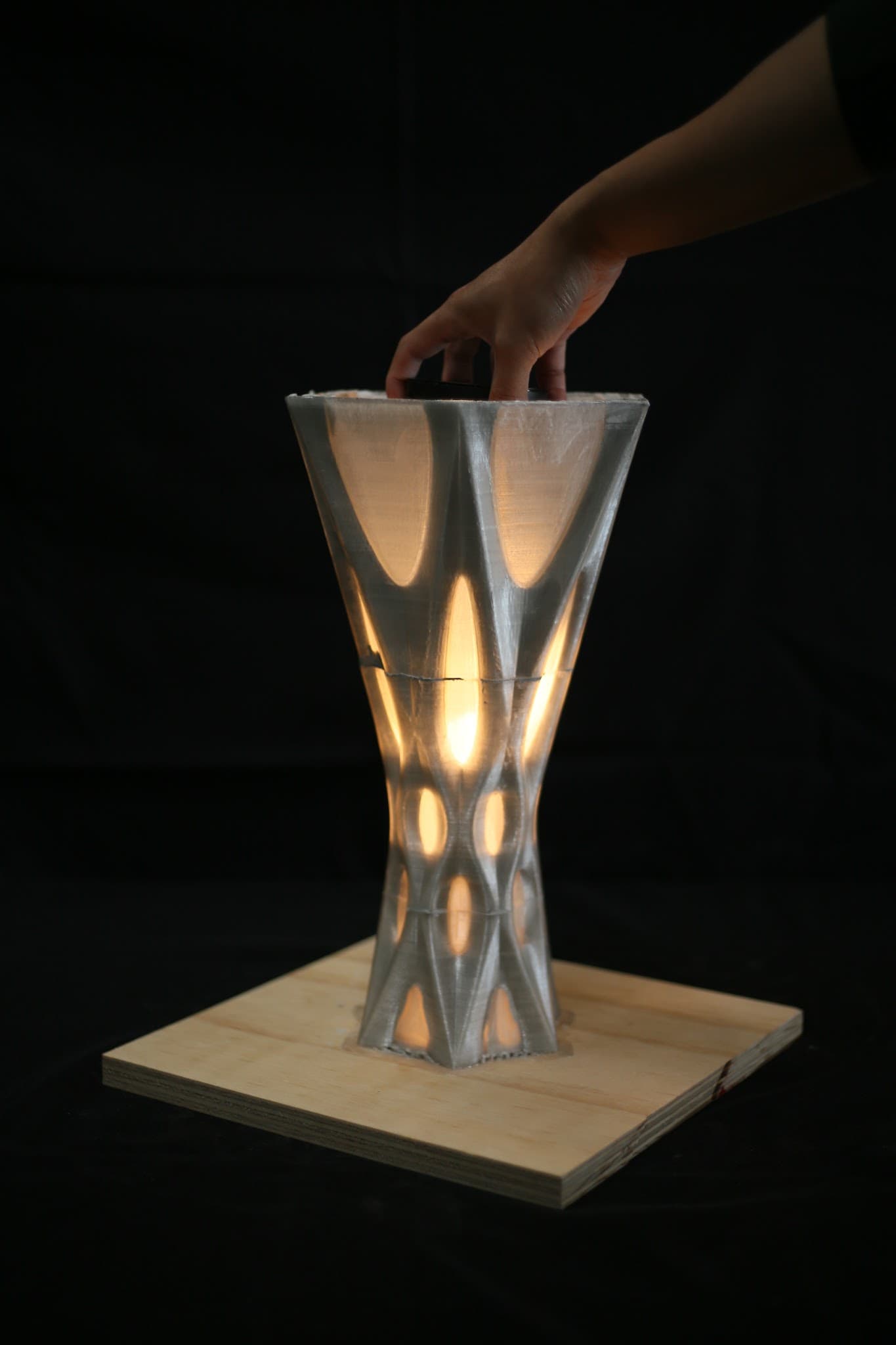
Robotic Printing Clay Formwork for Concrete Casting.
The project explores the design and construction of a tree truss structure, inspired by the organic and fluid geometry found in natural tree forms. These profiles exhibit elegance, hollowness, and structural fluidity, which became key design values. However, translating this vision into reality presents significant technical challenges, including geometric instability, material waste, and scale limitations when relying on traditional 3D-printing techniques. To address these challenges, we adopted an innovative approach that combines 3D-printed clay formwork with concrete casting. While direct 3D printing of the structure poses difficulties in achieving the desired Y-shaped geometry, clay formwork offers a practical solution. Clay can be precisely printed to create intricate forms, and its reusability after being dissolved in water ensures a sustainable production cycle. Once the segmented clay formwork is printed, concrete casting is used to fill and unify the structure, restoring its geometric continuity and enhancing structural integrity. The fluid properties of concrete allow it to adapt seamlessly to complex geometries, fulfilling the design's aesthetic and functional requirements. Furthermore, the reusability of clay formwork reduces material waste, aligning with principles of environmental sustainability. This method bridges the gap between design intent and material realization, overcoming the limitations of direct 3D printing. To validate our approach, we conducted a series of experimental phases. These included form-finding exercises to explore geometric possibilities, cylinder testing to optimize material properties, filament prototyping to evaluate structural behavior, and clay printing for real-scale construction insights. Six parallel experiments were carried out to identify the ideal sand-to-aggregate mix ratio for casting within clay formwork. Additionally, small-scale resin prototypes were produced to test final column geometries, and a 1:1 clay-printed section of the column was successfully realized to demonstrate the feasibility of the construction process. This integrated approach merges architectural design innovation with sustainable material practices and advanced fabrication techniques. By leveraging the adaptability of clay formwork and the structural performance of cast concrete, the project pushes the boundaries of architectural geometry and demonstrates a scalable method for constructing complex organic forms.